for PROFESSIONAL
難題を解決した経験を活かし1+1が3になるチームを創りたい
事業工場 技術開発部
技術グループ 第二チーム
チームリーダー
小島 卓
2008年入社
機械工学科卒業
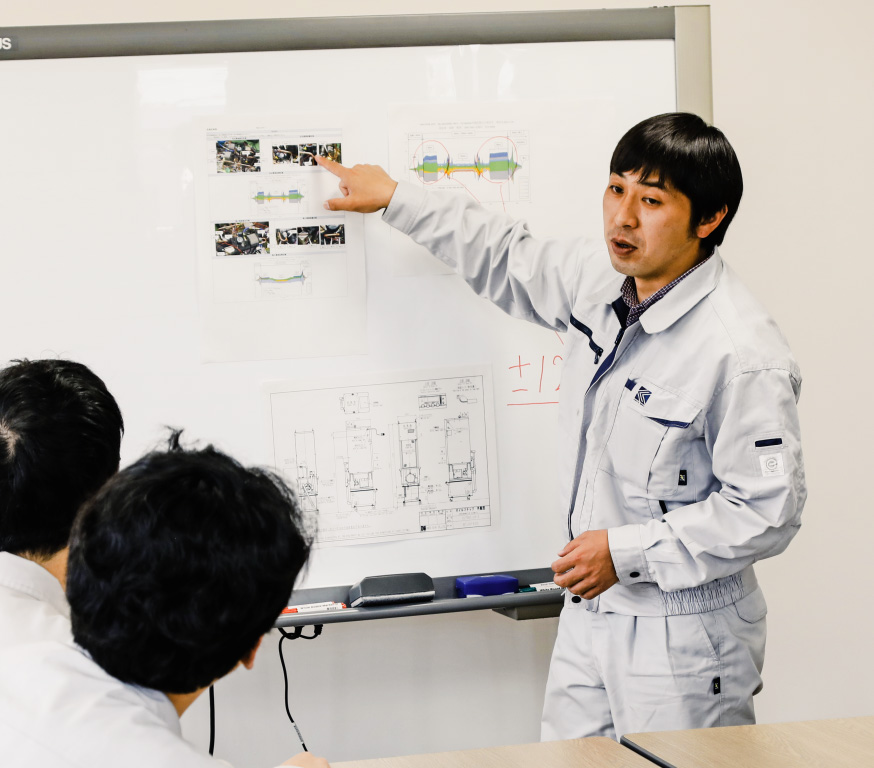
SUGURU KOJIMA
WORK STORY
人 × 技 術
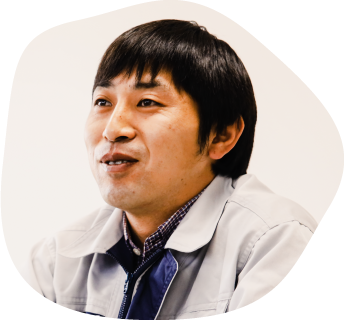
入社から現在までのキャリア
就職活動では、大学で機械工学を専攻したことから機械設計ができ、かつ部品ではなく機械装置そのものを手掛けられる会社を中心に活動。卒業研究でフロンの代替冷媒をテーマにしていたことから、地元でも希望通りの仕事ができる関東精機があることを知り入社を決めた。製造部門で半年間製造実習を経験し、技術グループに配属。工作機械向けの油温自動調整機を数年担当してから、半導体露光装置向けの液温自動調整機の開発プロジェクトに参加。以来、半導体製造装置向けを担当している。
CHALLENGE
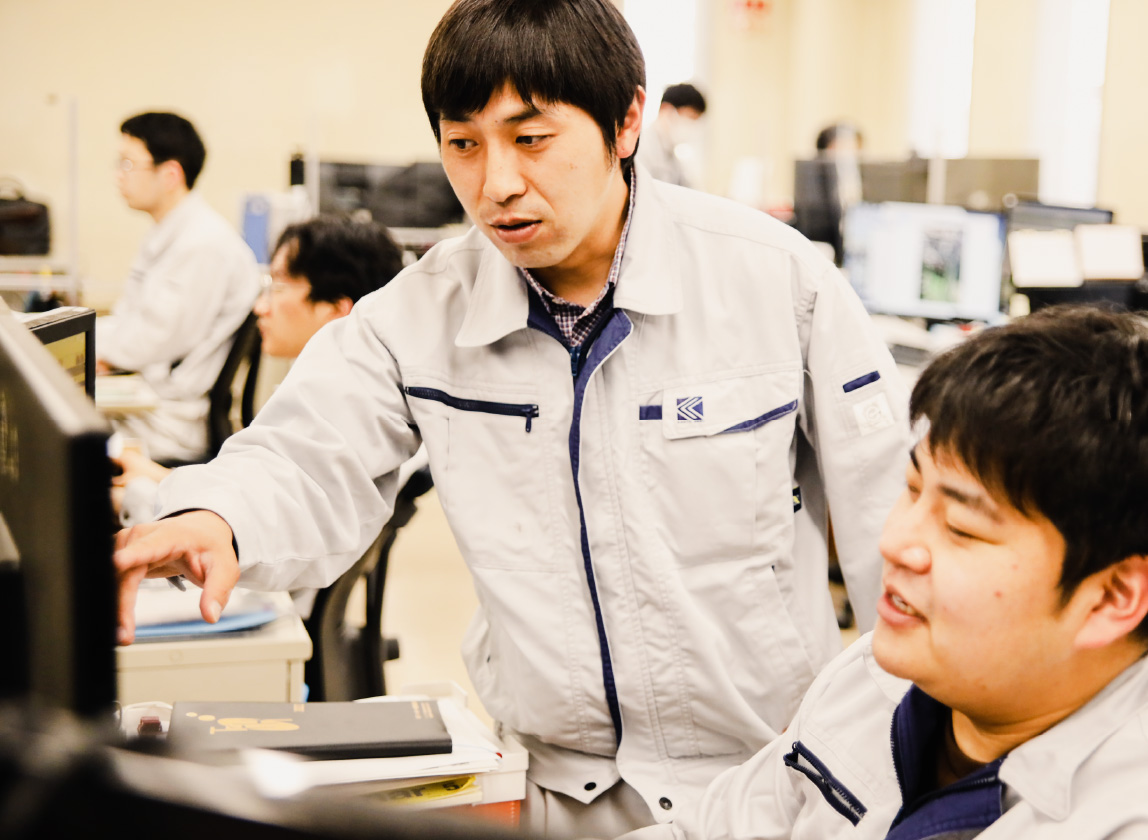
世界的な半導体メーカーの依頼で純水の純度を下げない装置の開発へ
「オイルマチック」と並んで、水や純水を熱媒体として使用する「ピュアマチック」も、当社の主力ブランドのひとつ。支えているブランドとしては、半導体製造装置や医療器械、リニアモーター等になります。なかでも、私が担当しているのは半導体製造装置向けです。オイルと水は、粘度や伝熱率等に違いがあること、そして半導体業界は要求仕様が非常に細かいなど工作機械向けとはまた違った難しさを感じています。
その中で、印象に残っているのは世界的な半導体メーカーで使われる「ピュアマチック」を手掛けたときのことです。お客さまからの一番の要望は、「純水の純度を下げない装置を開発してほしい」というものでした。通常、タンクにはステレンスを使用しますが、そのままだと微量ながら金属イオンが溶け出し純度を下げることになります。この難問をどう解決するか。開発はトライ&エラーの繰り返しになりました。
SOLUTION
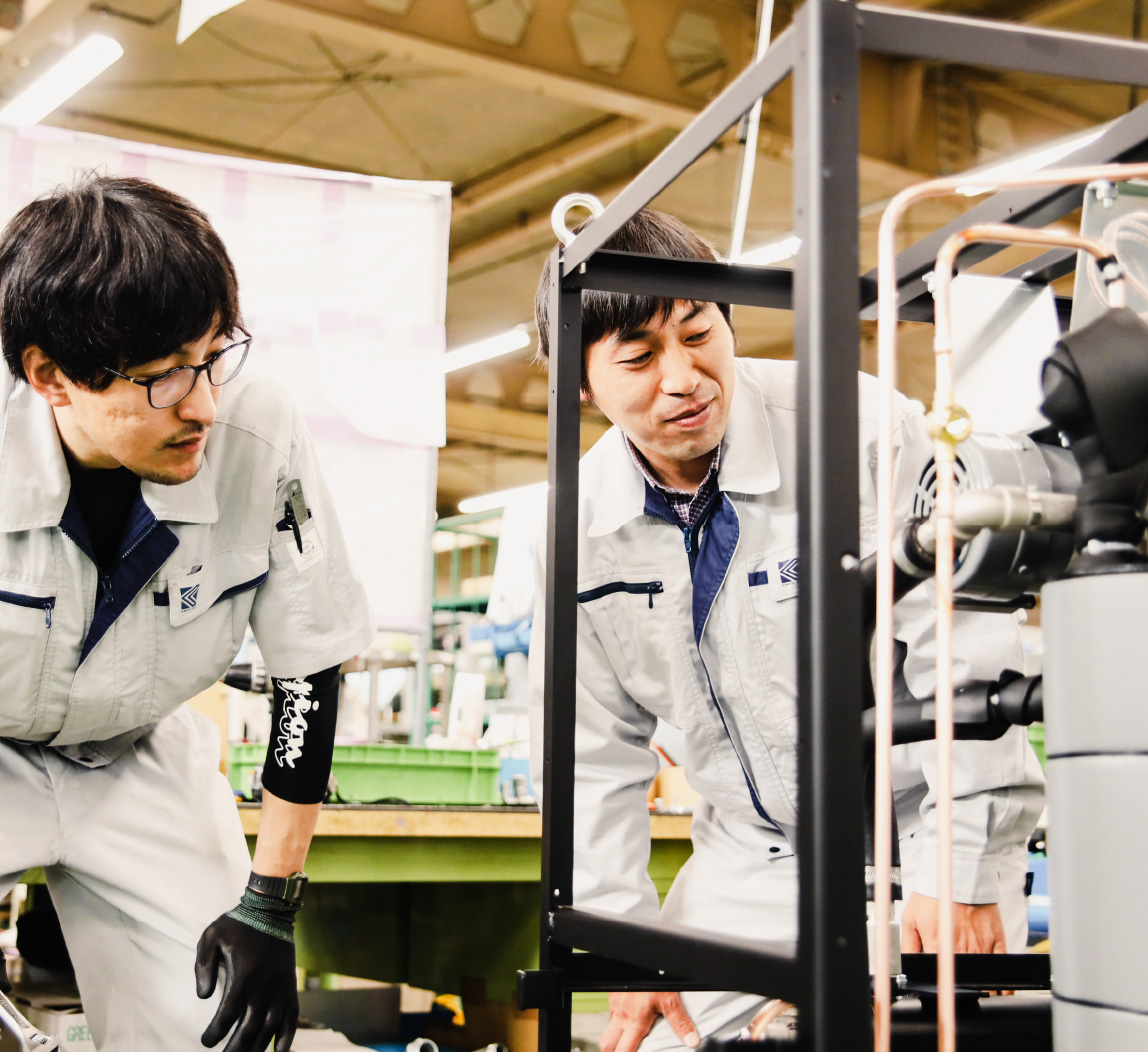
社内外から最大限の協力を得て、コーティングや板金の問題を解決
まず考えたのがタンクの材質を、金属イオンが溶け出さない樹脂系に代えることです。しかし、このアイデアは耐圧性に難がありました。半導体製造装置向けで一番のリスクと言える漏水(感電の原因)の問題をクリアできなかったのです。結果、行き着いたのがタンクの内部をコーティングすること。ただ、コーティングについては当社でも初めての試みで、知見がまったくありませんでした。
そこで、実績のあるコーティングメーカーを見つけるところからスタート。綿密な打ち合わせの上、コーティングの膜厚が均一になる形状のタンクを設計・試作しました。膜厚にムラがあると、容器破損のリスクが高くなるのです。また、板金の問題もありました。溶接した個所から油分が漏れだすリスクもあったのです。これらの難問をクリアして無事納品できたのは、社内外から最大限の協力を得られたからと言えます。
振り返れば、半導体露光装置向けの開発プロジェクトでは、リーダーの手腕やチームワークの大切さを実感しました。この貴重な経験を活かして、私も1+1が3にも4にもなるチームを創っていきたいと思っています。